
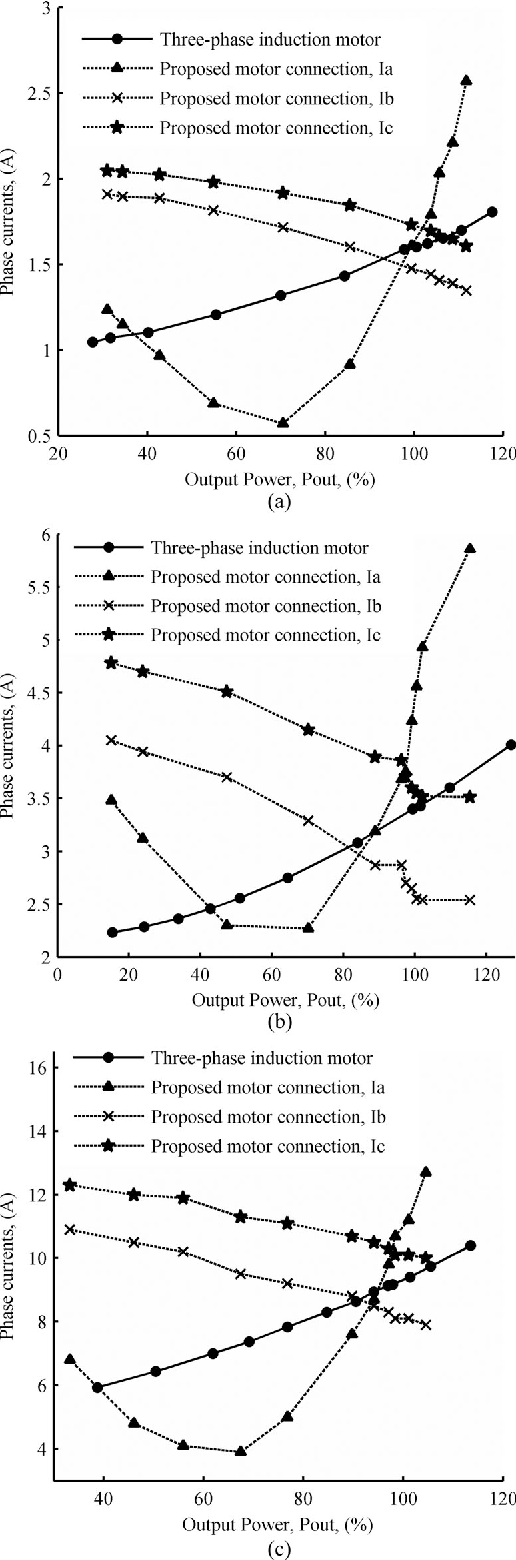
As a result, a weak revolving field is produced which starts the motor. Therefore, the currents I s and I m in the two windings have a reasonable phase difference of about 25° to 30° between them. When the starting winding of the motor is connected to the source of single-phase AC supply, the starting winding carries a current I s while the main winding carries a current I m as shown in the connection diagram.Īs the starting winding is made highly resistive whereas the main winding highly inductive. The starting and the main windings are so designed that the starting winding (S) has a high resistance and relatively low reactance while the main winding (M) has relatively low resistance and high reactance so that the currents flowing in the two windings have reasonable phase difference (α) of about 25° to 30° as shown in the phasor diagram. The starting winding operates only during the brief period when the motor starts up. The starting winding is displaced by 90° from the main winding as shown in the figure.
#Single phase motor winding connection series#
In this configuration each phase is brought to two coils that are connected in series with the other phases coils.A split-phase induction motor is a type of single-phase induction motor in which the stator is provided with a starting or auxiliary winding (S) and a main or running winding (M). In this configuration, each phase is brought to centre connection of two coils and to the end connections of each of the other two groups of coils. In this configuration, each phase is brought to two coils that are connected in series with one another. Terminals 4, 5, and 6 are tied together to make a second neutral connection. In this configuration, each phase is brought to two coils that are connected in parallel with each other. It is important to note that these points represent the internal connection of the coils of the motor, not how they are to be hooked up to voltage. If it is Delta wound, each of wires 1, 2, and 3 should have continuity with two other leads: The three leads without continuity to wires 1, 2, and 3 should all have continuity with each other. If it is Wye wound, each of wires 1, 2, and 3 should only have continuity with one other lead (4, 5 and 6 respectively).
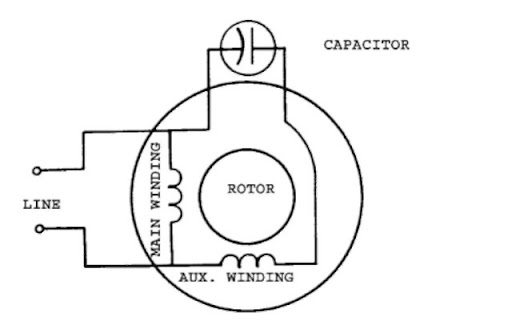
By using an ohmmeter to do a simple continuity check, you can determine the construction type of the motor. If a Wye wound motor is connected as a Delta wound motor or vice versa, the motor will not operate properly.Ĭonsider this situation: You have nine leads coming from a motor, but no indication of whether its Wye or Delta wound. It sometimes becomes necessary to test or confirm the configuration of a motor before final connection. These leads are numbered 1–9, and in both Wye and Delta follow a standard numbering convention: starting at the top of the diagram with wire number 1, draw an inwardly descending spiral from each connection point, ascending to the next number at each step.ĭepending upon the internal construction of the motor, these leads can be hooked up in one of four ways: High- or low-voltage Wye, or high- or low-voltage Delta Identifying Wye or Delta with an Ohmmeter In both the Wye and Delta configurations, three of these leads are connected internally, and so only nine leads are brought out of the motor for connection. It is important to size motor starters and their overload relays based on the expected value of current that is to be drawn by the motor at the voltage it is used at.Įach of the six individual coils has two leads supplying it, for a total of twelve leads in total.
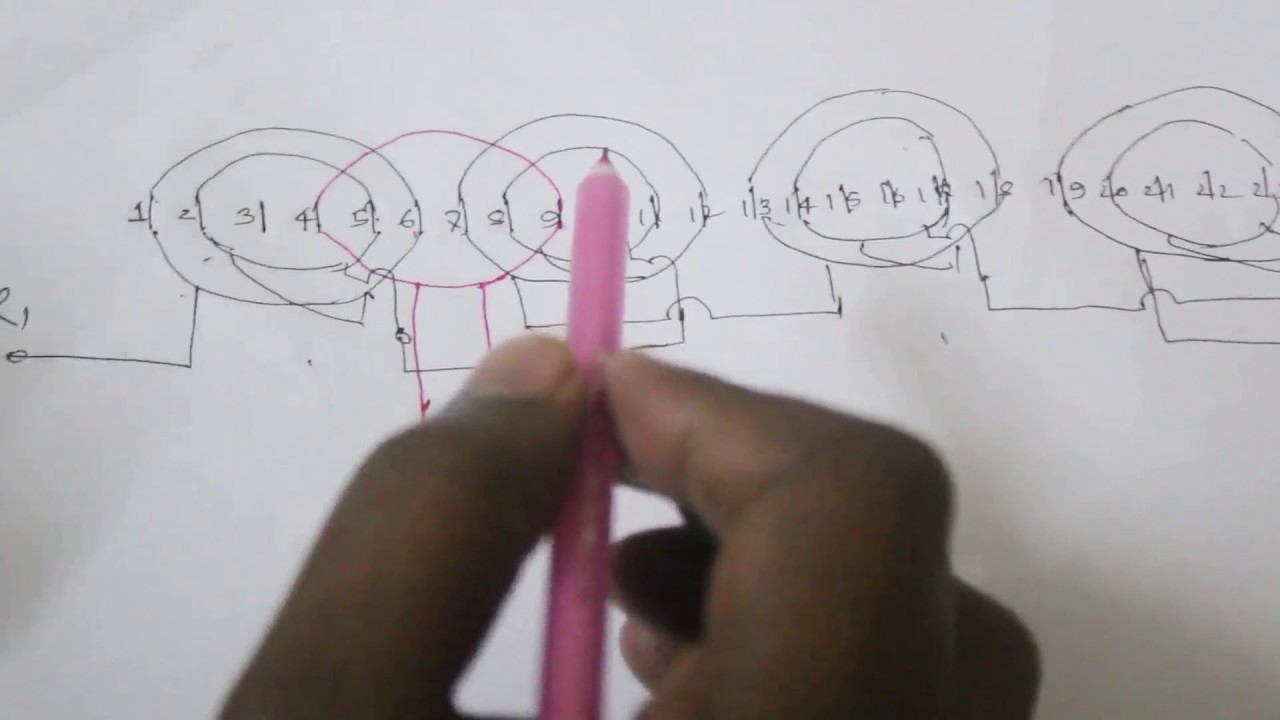
Most motors will list two values of voltage and current on their nameplates. Note that the low-voltage connection will necessarily need to draw twice as much current from the source as the high-voltage connection. In the low-voltage configuration, the two coils of each phase are connected in parallel with each other so that the lower value of supply voltage is shared equally between the coils and rated current is drawn through each winding. In the high-voltage configuration, the two coils of each phase are connected in series with each other so that the higher value of supply voltage is split equally between them and rated current is drawn through each winding. Three-phase motors are also constructed to operate at two different voltages, and so the coils can be connected in either their high-voltage or low-voltage configurations. There are two classes of 3-phase motors: Wye and Delta. The internal construction and connection of these coils inside of the motor is predetermined when the motor is manufactured. Standard 3-phase motors use six individual coils, two for each phase. Three-phase motors use coils of wire to create magnetic fields and produce rotation.
